Walcowanie blach to ważny proces w przemyśle metalowym i produkcji. Polega na mechanicznym formowaniu metalu, który przechodzi między dwoma obracającymi się wałkami. W efekcie blacha otrzymuje określoną grubość i kształt, od cienkiej folii po solidne arkusze, z gładką powierzchnią i wysoką wytrzymałością.
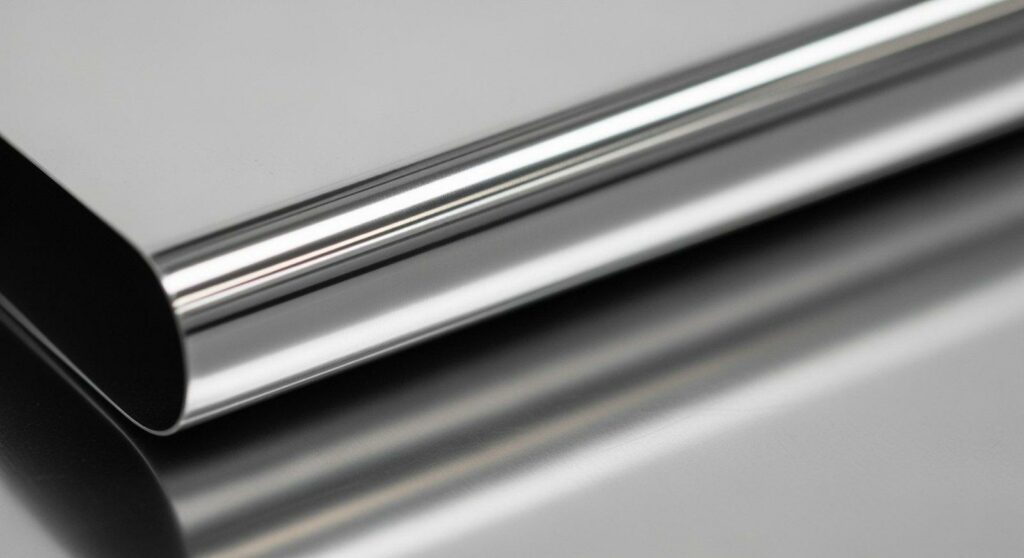
To sprawia, że walcowanie jest popularne w wielu branżach – samochodowej, budowlanej i wielu innych. Aby dowiedzieć się więcej o tej technologii, odwiedź walcowanie blach.
Walcowanie sprawdza się w wielu przypadkach. Można dzięki niemu produkować cienkie oraz grube blachy, profile o różnych kształtach czy rury. Możliwe są dwa główne rodzaje tego procesu – na gorąco i na zimno.
Wybór zależy od wymagań stawianych gotowemu wyrobowi – od wymiarów, po własności mechaniczne i wygląd powierzchni. Co więcej, walcowanie zmniejsza ilość odpadów, co pozwala zaoszczędzić materiały i pieniądze oraz ogranicza wpływ na środowisko.
Lepsze właściwości mechaniczne i wygląd powierzchni
Walcowanie blach mocno poprawia właściwości mechaniczne metalu. Podczas zgniatania struktura staje się gęstsza, co podnosi twardość i wytrzymałość materiału.
Walcowanie na zimno jeszcze bardziej zwiększa te cechy, dzięki czemu stal staje się bardziej odporna na zginanie czy rozciąganie. Z tego powodu blachy walcowane na zimno są wykorzystywane tam, gdzie trzeba dużej dokładności oraz trwałości – na przykład w częściach samochodów, samolotach czy sprzęcie elektronicznym.
Kolejną rzeczą są bardzo gładkie i równe powierzchnie uzyskiwane podczas walcowania. Przy blachach walcowanych na zimno powierzchnia jest wyjątkowo gładka, bez zanieczyszczeń czy nalotów. To ważne tam, gdzie liczy się wygląd i funkcja, na przykład w elementach dekoracyjnych lub miejscach, gdzie trzeba zmniejszyć tarcie.
Wyższa wydajność i mniejsze koszty produkcji
Walcowanie to bardzo wydajny sposób przetwarzania metali. Umożliwia szybkie przygotowanie dużej ilości materiału, ograniczając odpady do minimum. Jest tańszy niż inne metody, jak frezowanie czy cięcie, gdzie strata materiału jest większa.
Nowoczesne maszyny do walcowania (często sterowane komputerowo, CNC) gwarantują powtarzalność i wysoką precyzję w produkcji seryjnej. Automatyzacja obniża także koszty kontroli jakości. Wszystko to sprawia, że walcowanie blach jest korzystnym wyborem dla firm chcących produkować szybko, tanio i w dużych ilościach.
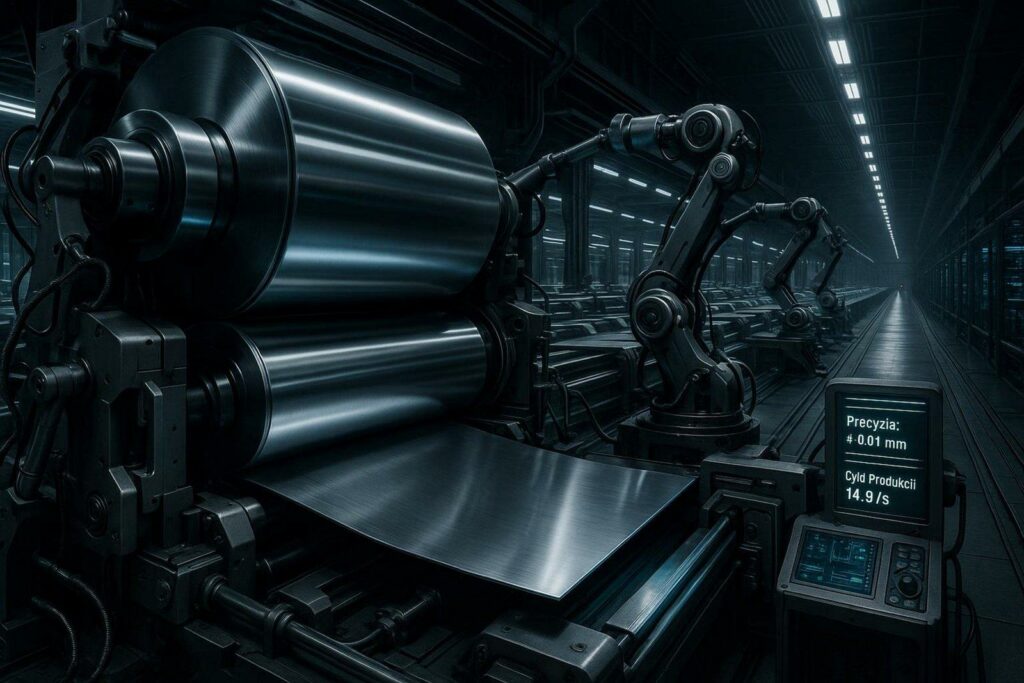
Duża swoboda kształtowania i różnorodność produktów
Jedną z największych zalet walcowania jest możliwość łatwego dostosowania wyrobu do potrzeb. Można wytwarzać zarówno proste, płaskie blachy, jak i skomplikowane profile, rury o różnych kształtach, stożki lub elementy o nietypowych krzywiznach.
Zaletą są różne techniki walcowania (na gorąco i na zimno) oraz typy maszyn (walcarki duo, trio, czterowałowe czy wielowałowe), dzięki czemu każdy producent może dobrać sprzęt i sposób pracy do wymagań klienta i przeznaczenia produktu.
Zaleta | Korzyść |
---|---|
Precyzja wymiarów | Jednolite grubości, dobra powtarzalność |
Elastyczność kształtów | Szeroka gama produktów, łatwość zmian rozmiarów |
Wysoka jakość powierzchni | Gładkość, brak pęknięć czy zanieczyszczeń |
Oszczędność materiału | Mniej odpadów, tańsza produkcja |
Lepsze właściwości mechaniczne | Większa wytrzymałość i trwałość |
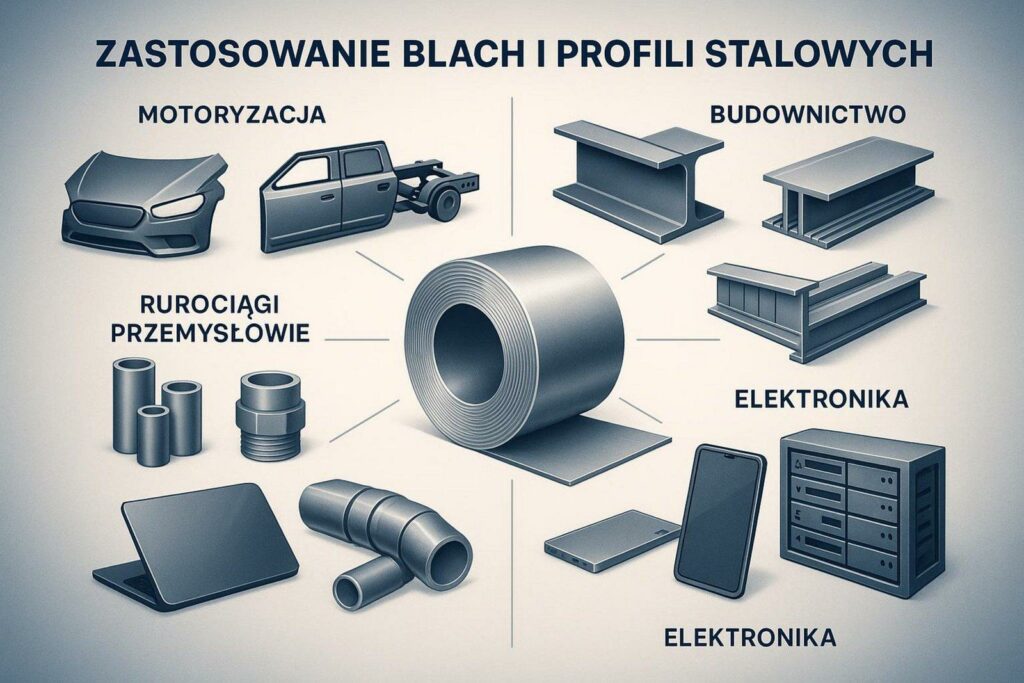
Dłuższa trwałość i niezawodność wyrobów
Odpowiednie parametry procesu walcowania (temperatura, prędkość, liczba przejść przez walce) pozwalają uzyskać materiały o odpowiednich właściwościach do konkretnego zastosowania. Blacha walcowana dobrej jakości ma równomierną strukturę i bardzo małe naprężenia wewnątrz materiału.
Brak naprężeń oznacza, że produkty nie pękają ani nie odkształcają się łatwo podczas długotrwałego użytkowania. To daje większą niezawodność i dłuższy czas użytkowania – szczególnie ważne w budownictwie, maszynach czy transporcie, gdzie bezpieczeństwo i solidność mają priorytet.
Jak walcowanie blach wpływa na jakość finalnego produktu?
Walcowanie bezpośrednio przekłada się na jakość gotowych elementów. Pozwala utrzymać stałe parametry materiału, zarówno jeśli chodzi o cechy fizyczne, jak i wygląd. Odpowiedni wybór rodzaju walcowania (zimne czy gorące) pozwala dopasować właściwości do zamierzonego zastosowania.
Na przykład: walcowanie na zimno daje najlepszą precyzję wymiarów i powierzchni, a walcowanie na gorąco najlepiej sprawdzi się przy większych konstrukcjach i tam, gdzie liczy się plastyczność materiału. Dzięki temu wyroby spełniają wysokie wymagania techniczne i jakościowe.
Równomierna grubość i struktura materiału
Jednym z podstawowych atutów walcowania jest uzyskanie blach o dokładnie tej samej grubości na całej powierzchni. Nowoczesne maszyny, zwłaszcza sterowane komputerowo, umożliwiają ciągłą kontrolę i formowanie metalu bez niedoskonałości czy zmian grubości. Jest to ważne np. przy produkcji rur czy elementów konstrukcyjnych.
Walcowanie także poprawia wnętrze metalu: zagęszcza strukturę i usuwa drobne defekty, jakie mogły powstać podczas odlewania. W trakcie walcowania na gorąco zachodzi także proces rekrystalizacji, który dodatkowo usuwa wewnętrzne naprężenia. Dzięki temu wyroby są stabilne i ich właściwości stałe w czasie.
Większa odporność na odkształcenia i uszkodzenia
Dzięki walcowaniu blachy są mniej wrażliwe na trwałe odkształcenia. Proces zgniatania na zimno podnosi twardość i wytrzymałość materiału. Blachy walcowane na zimno są bardziej odporne na rozciąganie, zginanie i wszelkie obciążenia mechaniczne.
Precyzja procesu dodatkowo zmniejsza ryzyko wad czy pęknięć, a wysoka jakość powierzchni chroni metal przed korozją, zarysowaniami czy innymi uszkodzeniami. Dzięki temu produkty walcowane nie tylko dobrze wyglądają, ale także są trwałe i pewne nawet w trudnych warunkach pracy.
Norbert jest doświadczonym redaktorem specjalizującym się w tematyce ekonomii, finansów i zarządzania. Pasjonuje się analizą rynków finansowych oraz nowoczesnymi strategiami biznesowymi. Prywatnie miłośnik literatury ekonomicznej i aktywnego stylu życia, lubiący dzielić się wiedzą i inspirować innych do świadomego zarządzania swoimi finansami.
Dodaj komentarz